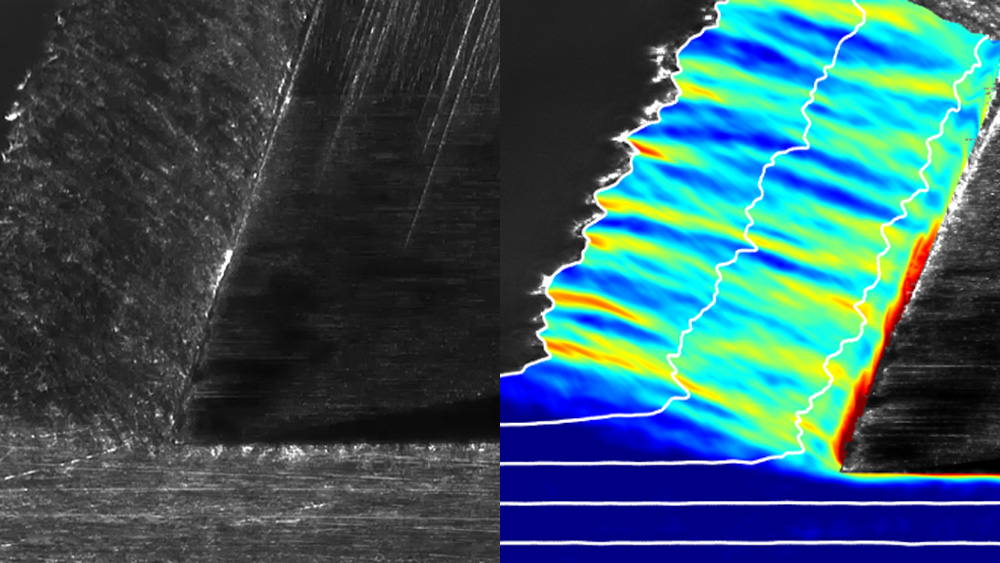
Researchers at Texas A&M University are taking a traditional manufacturing tool — metal cutting — and developing a more accessible method for understanding the behavior of metals under extreme conditions.
Metal cutting – scraping a thin layer of material from a metal's surface using a sharp knife (not unlike how we scrape butter) – might not be the first thing that comes to mind for studying material properties. However, Drs. Dinakar Sagapuram and Hrayer Aprahamian, assistant professors in the Wm Michael Barnes '64 Department of Industrial and Systems Engineering, wanted to see if the process could predict material behavior under various deformation conditions. Their team included Harshit Chawla, an industrial and systems engineering doctoral student, and Dr. Shwetabh Yadav, an assistant professor at the Indian Institute of Technology Hyderabad.
“The knowledge of how materials deform and fail under harsh mechanical conditions is vital for studying and developing various technological applications, including manufacturing processes, crash testing of vehicles and impact testing for defense-related applications,” Chawla said.
Because the cutting process involves locally shearing or deforming the metal to extreme levels under high rates, the team hypothesized that it could provide fundamental information on the material's strength, resistance to plastic deformation or irreversible shape change.
"The research opens a new and interesting application for metal cutting as a 'property test' that material scientists and physicists can use to test their theories," Sagapuram said. "The number of mathematical theories of metal plasticity under high strain rates far outstrips the experimental data. So, the property information obtained using metal cutting can test which theories are valid and which are not."
The team uses a high-speed camera to observe how metals deform and shear when they encounter a sharp cutting tool and then use this information to deduce their basic property information. A significant challenge, however, lies in obtaining intrinsic material properties from the visual high-speed imaging data. While metal cutting is not Aprahamian's area of expertise, the partnership with Sagapuram has generated new ideas and numerical techniques.
"An important aspect of this research is to establish mathematical optimization techniques that guarantee global optimality, thereby achieving the best possible solution," Aprahamian said. "Otherwise, you might obtain solutions that seem satisfactory, but they don't accurately describe the material."