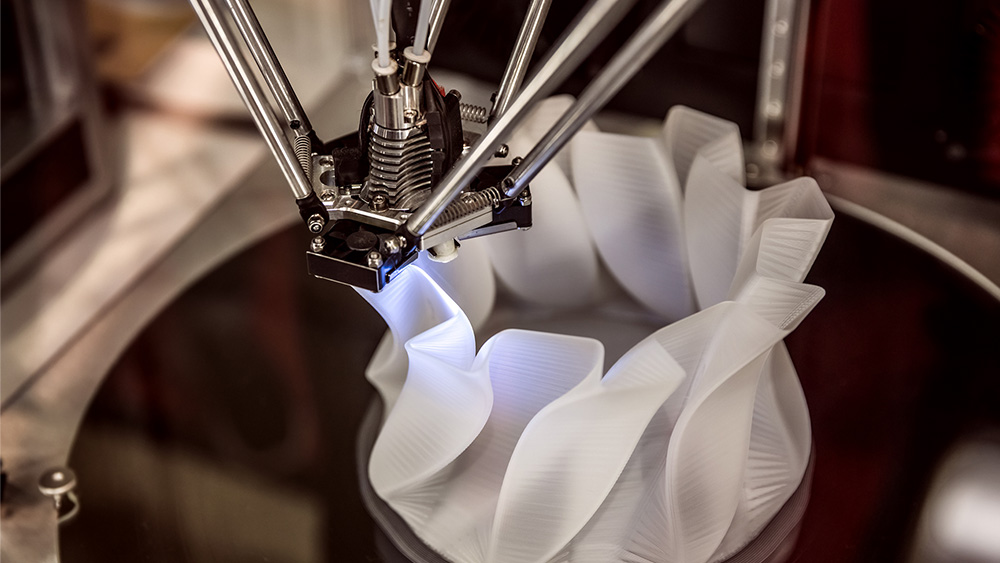
While advanced manufacturing provides increased access to product replication and the agility to pivot when the product needs to be changed, the risk for counterfeit production rises. SecureAmerica Institute (SAI), Texas A&M Engineering Experiment Station (TEES) researchers and their partners at New York University (NYU) are developing techniques that successfully embed markers into 3D-printed products so customers can verify that items received are not counterfeit. This research is part of SAI’s nationwide project call to empower a secure and resilient domestic manufacturing enterprise.
Manufacturing-as-a-service (MaaS) connects designers, manufacturers, customers and consumers, streamlining the process from design to delivery. This widely accessible technology also creates added layers of vulnerability and opportunity for counterfeit product dissemination.
“The risk of counterfeit products for items like automotive parts, electronics, safety equipment and medicine are of particular concern, especially with increased MaaS technology use,” said Dr. Ramesh Karri, professor, co-founder and co-chair of the NYU Center for Cybersecurity, and principal investigator for this project. “Identifying techniques that reduce these risks will protect manufacturers, customers and consumers as we ensure product needs are met safely.”
The global market for advanced manufacturing is expected to grow from $19.5 billion in 2021 to $56.1 billion by 2026, indicating a greater need for built-in security measures for domestic manufacturing. In addition, physical supply chains are being supplanted by cyber-enabled smart manufacturing supply chains where digital objects are transmitted via shared cloud storage, then transformed into physical objects at the place and time of need. This project outlines how to enhance and test cybersecurity while assuring that it is considered and built into manufacturing systems.
The technique of embedding unique signatures within the 3D-printed product begins with design files and a trusted pool of registered manufacturers within the MaaS platform.
“Intrinsic signatures provide anti-counterfeit marks in the final product, making it much more difficult for the part to be reverse engineered,” said Dr. Satish Bukkapatnam, director of the TEES Institute for Manufacturing Systems and professor in the Department of Industrial and Systems Engineering at Texas A&M University. “Customers can validate that their product was manufactured from an authentic design source by comparing the embedded signature from the MaaS platform to the scanned signature of the products received.
“The manufacturing process itself plays an important role in implementing this technique,” said Bukkapatnam. “How products are manufactured determines not only how and what type of signatures can be created or embedded, but also how precisely those markers can be placed. These manufacturing-related aspects have not been considered in many earlier studies.”
Within the MaaS platform, each step leading to a product being manufactured is automated once a customer initiates a request. The appropriate design files are chosen and then shared for production, where both the designer and manufacturer are registered as authentic parties within that MaaS platform. A “key” indicating the unique identifiers is then shared with the customer when production begins so the authenticity comparison can be completed at delivery.
To test the reliability and scalability of their project, the research team completed a red-team-blue-team exercise, where the red team represented bad actors and the blue team represented the network of defense. Within two datasets — including 4,440 models and six different types of defects — the blue team used statistical analysis and machine learning to successfully identify the faults introduced prior to printing.
“We know the vulnerabilities within manufacturing cyberphysical systems and the feasible defense strategies we can deploy to protect the integrity of goods produced using smart manufacturing,” said Dr. Nikhil Gupta, professor at NYU-Tandon School of Engineering. “Now we have the framework and testbed to support manufacturers in stress-testing their legacy and emerging smart manufacturing standards, components and systems for built-in security.”
SAI will be able to offer this red-team-blue-team testbed as a service for small- to medium-sized enterprises and U.S. smart manufacturing partners at-large. In addition to developing and testing the feasibility of embedded signatures, the TEES research team explored the use of explainable artificial intelligence- (XAI) infused scanning to more efficiently detect internal markers. Using ultrasound imaging, scanning was completed faster and with an accuracy rate of more than 80%. Detecting internal signatures remains an area of research focus as current methods are either too expensive, too slow or not precise. This XAI-infused ultrasonic inspection technique is now in the process of being patented to help support this area of need for internal signature detection.