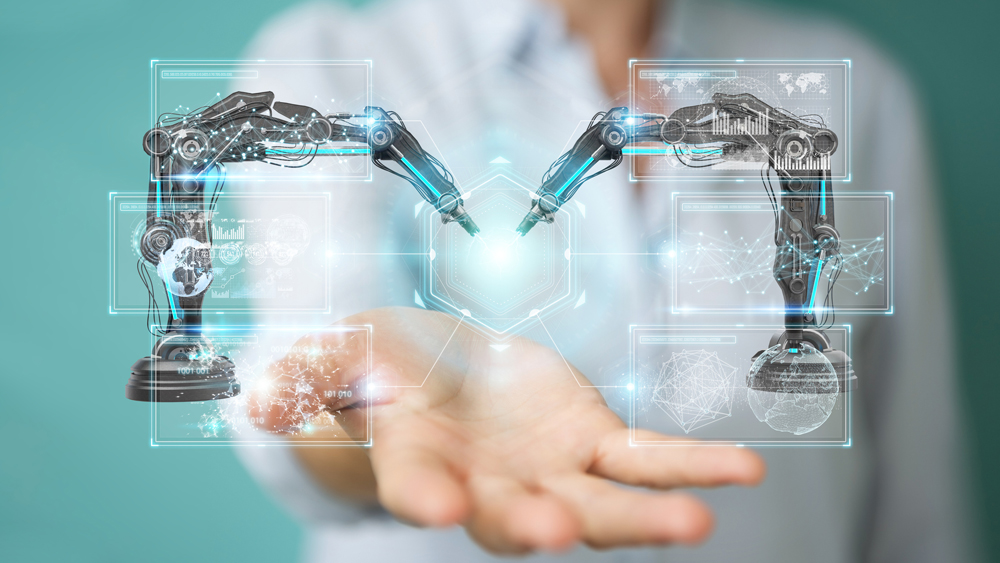
The COVID-19 pandemic exposed the inability of national supply chains to quickly shift production and reconfigure their logistics networks to meet customer demand surges during major disruptive events. The desperate scramble for items such as ventilators, face masks and even toilet paper won’t soon be forgotten, but the recent baby formula shortage points to a larger underlying problem with a supply chain model that prioritizes being efficient and cost-effective without accommodating the additional needs for resilience and robustness. But what if it was possible to proactively plan, and reactively respond and recover as quickly as possible following a supply chain disruption by further employing automation and robotics at key stages of the supply chain?
In response to recommendations outlined in the “Report of the Defense Critical Supply Chain Task Force,” the SecureAmerica Institute (SAI) and the Advanced Robotics for Manufacturing (ARM) Institute are partnering with industry leaders like General Electric (GE) to make targeted supply chain improvements. The Robotics and Automation Decision framework for Agility and Resilience (RADAR), which is funded by the U.S. Department of Commerce’s National Institute of Standards and Technology (NIST), plans to demonstrate the power of strategically adopting robotic and automation solutions across the supply chain. Led by Dr. Lefteris Iakovou, SAI’s manufacturing supply chain director and the Harvey Hubbell Professor of Industrial Distribution in the Department of Engineering Technology and Industrial Distribution at Texas A&M University, RADAR will demonstrate two-way visibility into and across critical supply chains to determine where the most impactful suppliers, vulnerabilities and interventions could exist following “black swan” disruptions like COVID-19.
Since over 98% of suppliers in the U.S. are small and medium-sized manufacturers (SMMs), according to the U.S. Census Bureau’s 2018 County Business Patterns Survey, establishing an understanding of what makes them more agile and cost-competitive is key to realizing the vision of this program.
“The utilization of flexible and collaborative robotics technologies to automate factory operations in the RADAR program has the potential for significant return on investments across multiple product lines, regardless of the size of the company,” said Dr. Prabhakar Pagilla, professor in the J. Mike Walker ’66 Department of Mechanical Engineering and associate dean for research in the Texas A&M University College of Engineering. “The RADAR program can uncover which characteristics and attributes companies should incorporate to increase their likelihood of successfully adopting robotics and automation in collaborative (human and robot) manufacturing environments.”
An imperfect understanding of existing constraints, incentives, opportunities and risks that can impact supply chains currently prevents many SMMs from fully embracing their technical innovation capabilities and contributes to end-to-end supply chain resilience. For instance, during some of the darkest days of the COVID-19 pandemic, large automobile manufacturers were able to pivot their production lines to produce ventilators. However, many SMMs lack the scale, know-how and support to fully explore their ability to be similarly agile. RADAR aims to productize the agile operational models of larger organizations so SMMs are also able to pivot as needed.
“During the COVID-19 pandemic, GE researchers developed a robust pandemic simulation of the supply chain volatility our industries experienced. We think that simulation can be applied in the RADAR project to enable more intelligent production management for future pandemics,” said Walter Yund, senior scientist in enterprise operations research at GE Research. “By merging GE Research’s pandemic simulation with existing hospital and COVID-19 supply chain data, this model could offer key insights for manufacturers to anticipate future demand and determine which elements of their supply chain are most at risk of a material shortage.”
Formalizing that decision-making process for SMMs also opens up more opportunities for cross-collaboration — not just in times of crisis but for innovation overall. SAI successfully demonstrated this idea on a small scale for rapid product development with the COVID-19 breathalyzer kiosk, which connected several seemingly disparate organizations and people to create a unique new technology during a time of need.
RADAR also seeks to redesign supply chains critical to the security of the nation without reverting to pre-pandemic practices. Bolstered by a framework of dynamically resilient, data-driven supply chain networks, RADAR will support the quick detection of disruptive events, efficient increasing of manufacturing capacity where needed and reduction of manufacturing capacity once recovery has been attained.
The defense industrial base looks holistically at the United States’ true manufacturing capabilities, so improving the resilience and competitiveness of the domestic supply chain will have national security implications. RADAR is on track to improve the resiliency, flexibility and competitiveness of SMMs — and is envisioned to enhance the resilience of the U.S. manufacturing industrial base when the next supply chain disruption materializes.
This research is supported by a $5 million grant from NIST. The funding is provided by the American Rescue Act and is part of a larger $54 million initiative by NIST to award high-impact projects for pandemic response research and development across eight manufacturing institutes in the Manufacturing USA network.