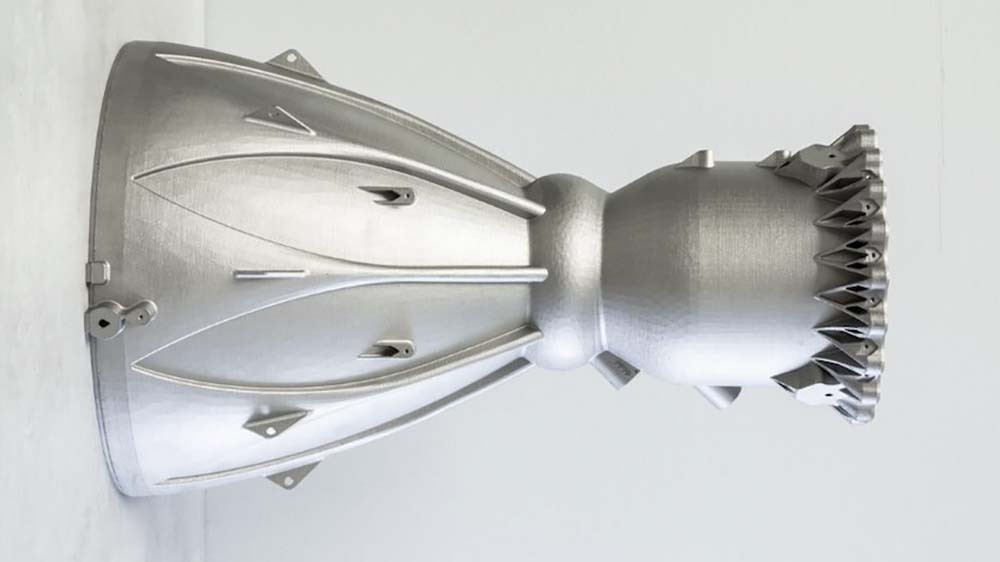
Hypersonic weapons travel at least five times the speed of sound and are critical to U.S. national security measures. Advanced innovation is required to keep this type of technology nimble and agile. That’s why the SecureAmerica Institute (SAI) partners at Ursa Major Technologies are exploring how additive manufacturing (3D printing) capabilities can enhance the production of hypersonic engines as part of a SAI nationwide initiative to empower a secure U.S. defense industrial base.
Propulsion systems are important components of hypersonic engines. These complex parts must work together seamlessly to ensure a high-performing and reliable system. According to research at Ursa Major, incorporating additive manufacturing into hypersonic production presents novel approaches to increase engine efficiency.
“3D-printing technology allows us to bypass the constraints of traditional manufacturing processes,” said Sabrina Ames, mission program manager at Ursa Major. “With additive technology, we can produce higher-performing fuel injectors and make fluid passages that mix fuel and oxidizer much more efficiently without adding significant mass to the parts.”
“Additive metallic manufacturing has the potential to address the critical need to create high-temperature parts with complex internal flow paths supporting the acceleration of propulsion engine design and technology,” said Dr. Erica Corral, associate professor at the University of Arizona and member of the governance board for the Texas A&M University Consortium for Applied Hypersonics. “Additionally, new opportunities for additive manufacturing of complex shape parts creates demand for research and development of reliable mechanical and thermal properties in these non-cast parts that are typically unique to their build and process.”
Ursa’s Major’s research focuses specifically on the 3D printing of small holes within propulsion systems that require small, intricate fluid passages. Creating more complicated passages was not possible before the introduction of additive manufacturing technology.
“It was significant for us to understand diversity between machines, vendors and print orientation when designing these components,” Ames said. “The geometry is also important. We needed to discern how repeatable these holes were given different types of print orientations.”
The research team began by experimenting with simple models and then moved on to more complex designs. “We created flat plates with holes first and then flowed those plates with a water flow rate developed in-house,” Ames said. “Next, we printed a rocket engine pre-burner for water flow testing.”
Ursa Major’s project discovered machine-to-machine variability and vendor-to-vendor variability when printing complex fluid passages were higher than desired.
“What will help us as an industry is to have more uniform flow coming out of the same parts,” Ames said. “Geometrically, the parts may be identical, but they flow differently because they print differently.”
“Consistently producing parts repeatedly across multiple machines in multiple facilities is the next step in unlocking the power of this technology to help an emerging market like hypersonics become sustainable,” said Chris Holshouser, SAI’s director of applied programs and strategic partnerships.
Ames said outcomes from the study are already strengthening different areas of the hypersonics industry. “Understanding this type of flow variation can help us anchor our designs. We are already using what we learned and putting it into action,” she said.