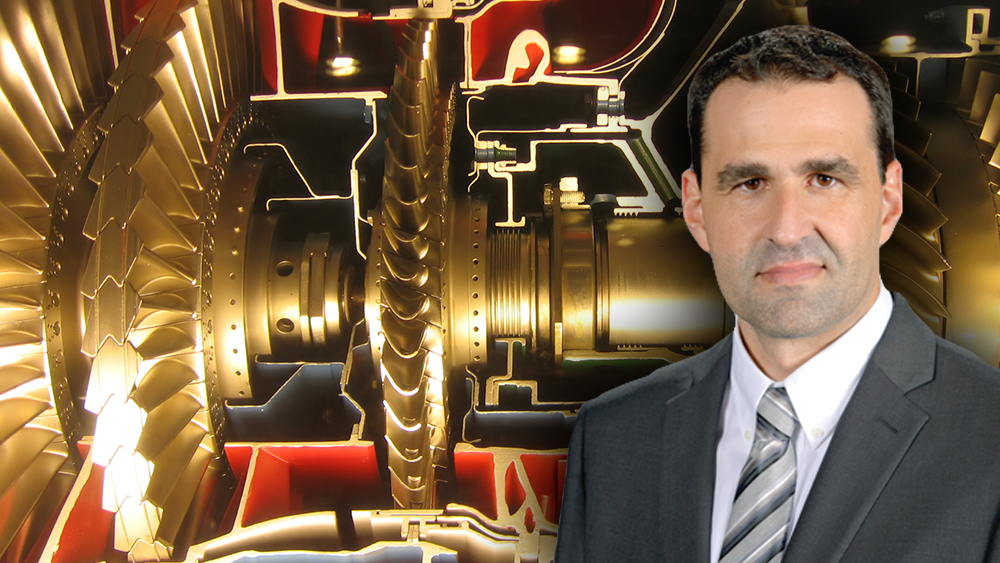
Turbomachinery is a crucial component in many applications requiring high power density equipment such as rockets, planes and power plants. A critical part of their success is the bearings that help keep their rotors spinning. Texas A&M University researchers are working to improve this rotation.
Advances in process fluid-lubricated bearings used in turbomachinery technology could lead to direct benefits for the power generation, oil and gas and aviation industries.
Dr. Adolfo Delgado, associate professor in the J. Mike Walker '66 Department of Mechanical Engineering, is working to increase the technology readiness level of these bearings by developing new designs and characterizing their performance — particularly those that use gas as the working fluid.
Delgado has published his research on this topic in the American Society of Mechanical Engineering Journal of Engineering for Gas Turbines and Power.
"We are currently looking at smart dampers for hybrid bearings and conducting system-level tests using a turboexpander dummy rotor," Delgado said. "We need to prevent contact between the rotor and the bearing surface while maintaining acceptable vibration levels as the rotor transitions through critical speeds."
Delgado said that while gas bearings themselves are not a new concept — they can be found in many applications, including dentist drills, gyroscopes, small power generation turbines and even air cycle machines in airplanes — their use in megawatt-class turbomachinery has not yet come to fruition.
"Gas bearings are currently used in many applications with a direct impact in our lives," Delgado said. "This technology will enable the development of higher power density turbomachinery able to reach higher speeds with a smaller footprint. Among other benefits, gas bearings will allow us to reduce the weight and footprint of turbomachinery while allowing operation at higher speeds and temperatures. In other words, gas bearings will enable the development of higher power density turbomachinery."
Delgado said the goal of preventing contact between the parts could be achieved by applying a damped flexible support alongside the gas film. However, this is the greatest challenge facing the bearing's progress toward being a viable replacement for oil-lubricated bearings.
"The most significant challenge that we still need to tackle is damping. As difficult as it may seem, we can easily levitate a 500 kg rotor with two gas bearings having a gas film of roughly 12 micrometers — a width thinner than a human hair," Delgado said. "That is not the difficult part, the actual challenge is to spin that rotor to 20,000 rpm while minimizing vibration levels and keeping the system stable."
Delgado’s research is currently supported by the Texas A&M Turbomachinery Research Consortium.