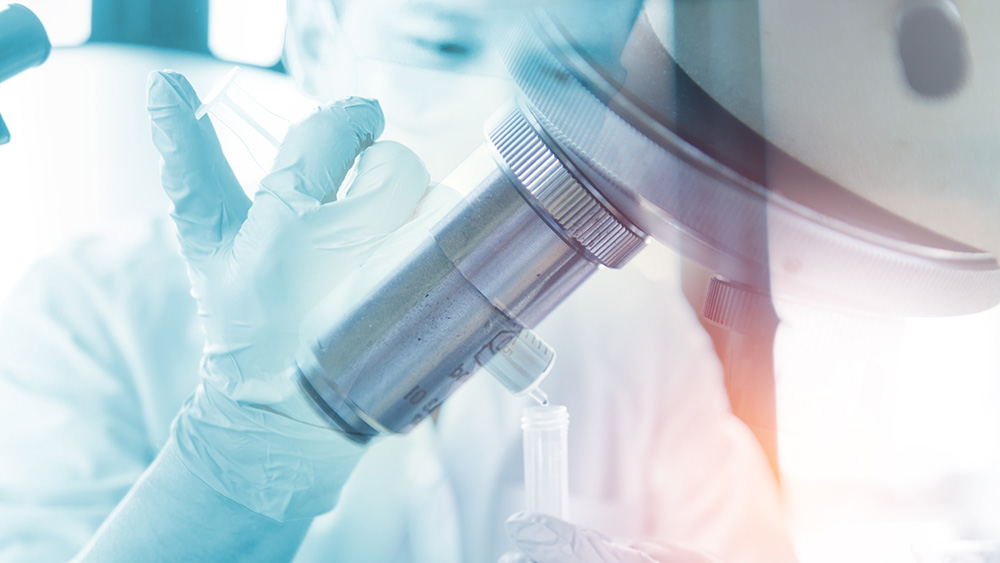
A new startup company that could profoundly change the sterility testing techniques of vaccines and other biopharmaceutical products has been launched with the support of the Texas A&M Engineering Experiment Station (TEES) Office of Commercialization and Entrepreneurship.
Formed in collaboration with Texas A&M University’s NanoBio Systems Lab (led by Drs. Arum Han and Paul de Figueiredo), HelioWave Technologies LLC is developing HelioSAFE, a fast, high-efficiency and automated sterility and bioburden testing system that uses lab-on-a-chip microfluidic-based approaches to detect contamination in therapeutics and therapeutic manufacturing workflows. The project is led by Dr. Adrian Guzman, chief technology officer and interim chief executive officer of HelioWave, and supported by Han, Presidential Impact Fellow, Chancellor’s EDGES Fellow and professor in the Department of Electrical and Computer Engineering, and de Figueiredo, professor in the Department of Microbial Pathogenesis and Microbiology.
The team is using a lab-on-a-chip miniaturization technology to provide a small chip-scale footprint where the embedded microfluidics technology provides low-cost and rapid testing to identify the presence of any living microorganisms in the solution being tested. This automated system ensures pharmaceuticals remain contamination-free and allows companies to identify and remove any contaminations in a timely and cost-efficient manner. Initial commercialization funds have been provided by the U.S. Department of Defense’s Small Business Innovation Research Program.
“Conventional sterility and bioburden testing systems utilize milliliter volume samples and days/weeks-long assays to test for sterility of therapeutic products, whereas HelioWave's technology uses micro-to-pico-liter (1,000 to 1,000,000 times smaller) sample volumes and can be conducted in hours/days,” Guzman said.
In addition, there are currently no real-time monitoring systems for sterility and bioburden testing of the intermediate and final products, which can lead to large batches of products being unknowingly contaminated during the biomanufacturing process, therefore requiring disposal, which can cost manufacturers greatly. HelioWave's technology also provides continuous monitoring that can be directly integrated in the therapeutic manufacturing workflow, providing manufacturers an additional tool to ensure their current production batch is free of any biological contamination.
“This significantly reduced testing time will allow potential sterility problems in the final product to be detected much faster, as well as help identify problems in the therapeutic manufacturing workflow earlier to mitigate any problem,” Han said. “The disposable lab-on-a-chip device can also significantly lower the cost of testing.”
The researchers are currently in the prototyping, characterization and validation stages of their lab-on-a-chip platform to ensure the system meets the required standards set by regulatory bodies. They are hoping to soon move into the pilot testing stage to demonstrate the enhanced performance of their system compared to conventional sterility testing methods, something they couldn’t have easily accomplished without support from the TEES Office of Commercialization and Entrepreneurship.
“Most technology platforms emerging from academia face significant barriers when it comes to reaching the market,” said Dr. Saurabh Biswas, executive director for commercialization and entrepreneurship at TEES. “Deep-tech ideas require significantly longer development time because of the interdisciplinary nature of the research, and also, significant capital is required beyond the basic R&D. Our office provides support during the early stages of research and development to enable continued product development and commercialization.
The commercialization and entrepreneurship office supports Texas A&M Engineering through its three groups: licensing and intellectual property management, venture creation and innovation programs, and strategic projects. They also provide support across the total life cycle of the innovation from its inception to intellectual property filing, prosecution process, licensing, venture creation and finally, working with external partners to enable commercialization of the technology.
“(Because of the TEES Office of Commercialization and Entrepreneurship), we are better positioned to bridge the gap from research and development to final production and mass fabrication of our chip for commercial use,” Guzman said.