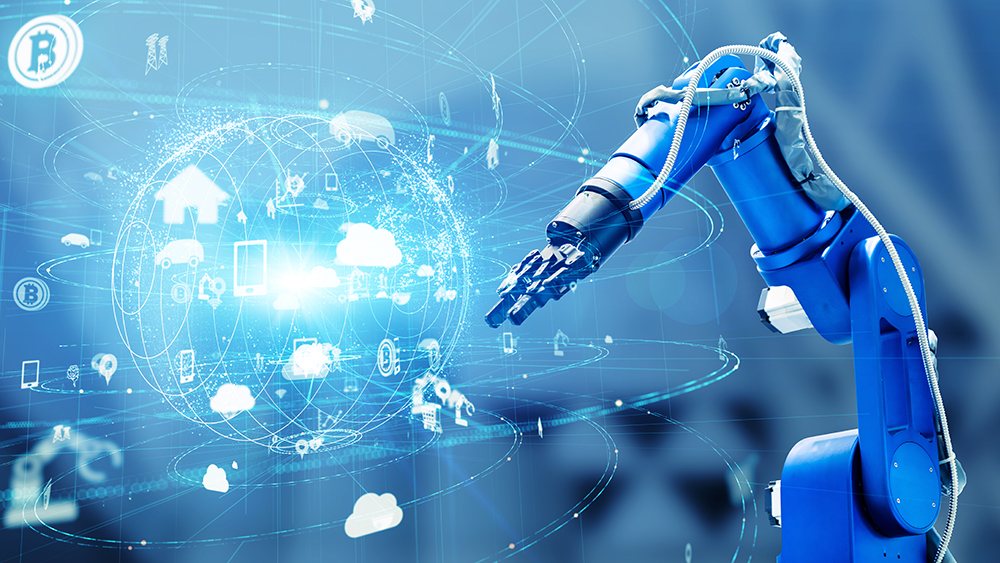
With the growing global concerns over climate change, scientists are looking for cleaner energy sources and other ways to minimize the carbon footprint in the world. Researchers at Texas A&M Engineering and the Ecole Nationale Superieure d'Arts et Métiers (ENSAM) are collaborating to look at the materials and products we use daily.
A carbon footprint is the total amount of greenhouse gas emissions that come from the production, use and end-of-life of a product or service. It is expected that in the next few decades there will be a major transformation in the materials used in civilian and military applications or in the aeronautics, automobile and other industries, and there will be a need to use materials and products that are more environmentally friendly.
Dr. Satish Bukkapatnam, director of the Texas A&M Engineering Experiment Station’s (TEES) Institute for Manufacturing Systems, and Dr. Mohamed El Mansori, professor in the Department of Mechanical, Materials Science and Manufacturing Engineering at ENSAM, combined their complementary strengths to advance the science and technology for biocomposite manufacturing to form the AM² transatlantic partnership. This partnership aims to effect change to a global manufacturing industry through extensive research collaborations, education programs, and mutual faculty and student exchange initiatives.
A biocomposite is a composite material formed by a matrix (resin) and a reinforcement of natural fibers. The matrix phase is formed by polymers derived from renewable and nonrenewable resources. Hemp, cotton, jute and flax are some common natural fiber reinforcements in biocomposites that have good mechanical properties.
“The work with Professor El Mansori was initiated to adapt methods for studying the machining process to create precisely shaped slabs of natural fiber composite materials for the emerging industrial applications,” said Bukkapatnam.
The interest in biocomposites is rapidly growing due to their great benefits. They can be used alone, or as a complement to standard materials, such as carbon fiber.
“A significant market driver for high-volume applications is the potential to disassociate material costs from the fluctuating price of oil and energy,” El Mansori said. “In many cases biobased materials offer weight reduction, added functionality, e.g., damping (restraining of vibratory motion) or impact absorption, and occupational health benefits.”
Prior to their collaboration, both Bukkapatnam, El Mansori and their respective teams had been studying components related to smart manufacturing with various materials systems and manufacturing processes for many years. In 2017 they combined their collaborative strengths: Texas A&M in smart manufacturing, focusing on advanced in situ sensing, and ENSAM’s strengths in multi-scale modeling and analysis, which led to several outcomes.
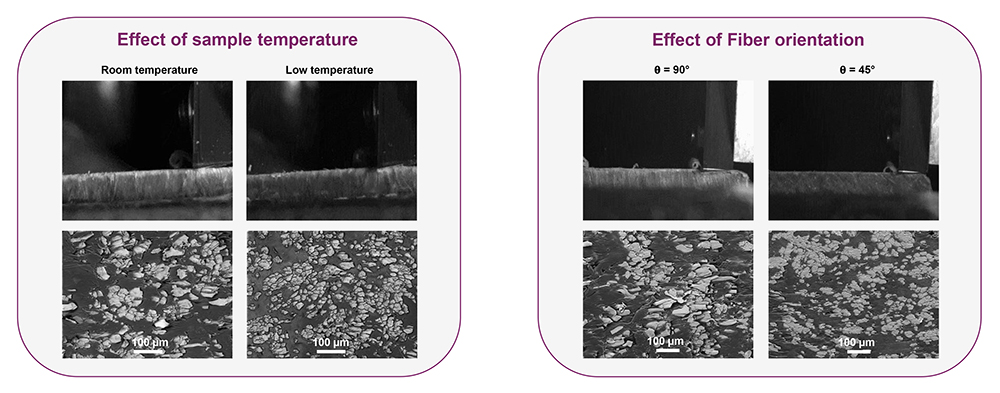
First was the creation of a smart experimental setup to study forces, vibrations and acoustic emissions generated during the machining of natural-fiber composite materials, and thereby using the signal patterns themselves to understand the physical phenomena underlying the way the material is removed from the surface of the composite material during the cutting process. This guided the setting of the various conditions such as the speed at which the tool should move the cut, the best orientation of the composite material to achieve an efficient cut and quality products. The work also led to the development of mathematical, finite element models to simulate how forces are generated during the cutting process and how they vary under the influence of the heat generated during the process.
El Mansori said biocomposites, especially those with long continuous fibers, present many challenges during near net-shape processing, where requirements include accurate dimensional tolerancing, drilling holes for assembly and controlled surface characteristics. Finishing operations such as machining or polishing are mandatory for fabricating the biocomposite part to meet service requirements.
However, finishing operations should not cause excessive damage in order to preserve the required industrial functionality of the biocomposite part (i.e., mechanical, frictional, thermal, acoustic or damping properties). The main damage source emanates from the severe contact between the abrasive tools and the biocomposite due to the high-generated tribological and thermal stresses. Addressing these challenges required expertise in multiple areas.
“Understanding the mechanism of the cutting process is essential for creating quality products, especially those of interest to the automotive industry,” Bukkapatnam said. “Besides the two of us, this research effort brought together the expertise of Drs. J.N. Reddy and Bruce Tai of mechanical engineering (at Texas A&M), and two project associates, Drs. Zimo Wang and Faissal Chegdani, who have since graduated and now serve as assistant professors in SUNY Binghamton, U.S. and Arts et Métiers, France, respectively.”
Because of the wide range of applications that exist for these natural composites, the impact of their research on cutting techniques can be enormous.
“Combinations of natural fibers and biobased polymers have been shown to have appealing composite properties, offering the enticing prospect that fully biobased composites are an increasing commercial reality,” El Mansori said. “Green image, weight savings, shorter cycle times, scratch resistance and above all, a lower (carbon) footprint are important factors for this development.”
Plus, the demand from designers, manufacturers and consumers for environmentally friendly products will inevitably drive the rapid development of other biocomposite materials and products as well. And future developments in fully biobased composites of consistent quality natural-fiber products could also be required at an affordable price in appropriate forms for composite molding and secondary mechanical processing technology.
“The next few decades will witness a major transformation in the materials that we use in our daily lives and for various applications,” Bukkapatnam said. “There will be a major push toward using materials and products that use a minimal carbon and economic footprint, and are environmentally benign. This research leverages Texas A&M’s initiatives in smart manufacturing to lead a major thrust toward smart, secure and sustainable manufacturing systems. These efforts are central to the current transatlantic partnership led by Texas A&M and Arts et Métiers.”