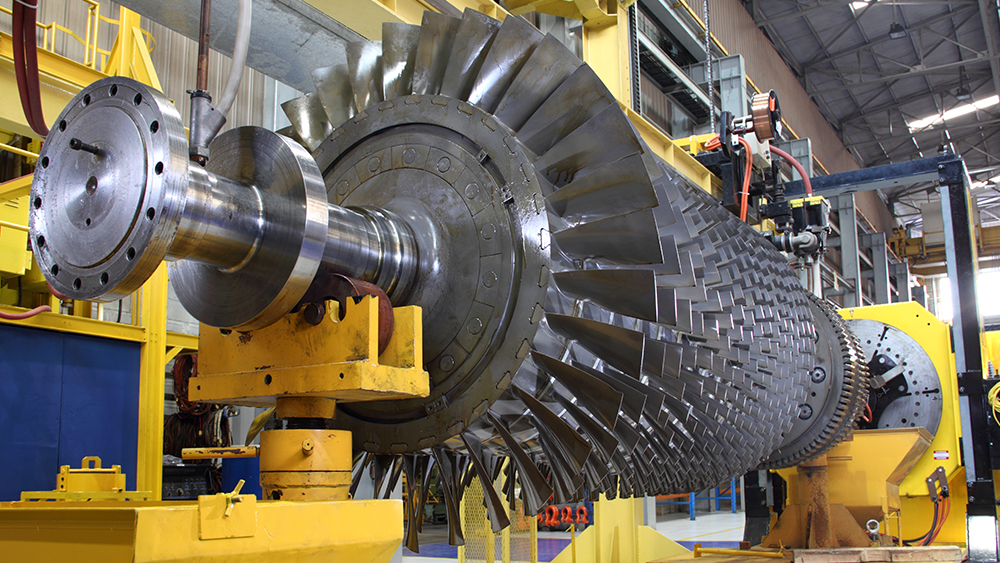
An essential component of engines used in aircraft and power generation is a gas turbine. The efficiency of these machines can be significantly amplified if they are made of materials that can endure harsh environments, such as high temperatures. These high-performance, futuristic turbines will have the potential to benefit not just the aviation and power industry, but also consumers by reducing their energy costs.
To develop such ultrahigh temperature-resistant materials, particularly those that can tolerate 1,300 C or at 1,800 C with coatings, the U.S. Department of Energy recently awarded $16 million to 17 projects as a part of Phase 1 of the Advanced Research Projects Agency-Energy’s (ARPA-E) Ultrahigh Temperature Impervious Materials Advancing Turbine Efficiency (ULTIMATE) program. A team led by Dr. Raymundo Arróyave, professor in the Department of Materials Science and Engineering at Texas A&M Univeristy, has received $1.2 million to investigate a class of metals, called refractory high entropy alloys (RHEAS), that can withstand higher operating temperatures.
“Finding a ‘printable’ refractory that would enable the next-generation ultra-efficient gas turbines is quite a scientific and technological challenge that will require that we at Texas A&M University and our partners at Brown University, Oak Ridge National Laboratory, Ames Laboratory and Thermo-Calc, Inc., push our scientific know-how to the limit. We are very excited to take on this project,” said Arróyave.
Arróyave’s project, “Batch-wise Improvement in Reduced Design Space using a Holistic Optimization Technique (BIRDSHOT),” aims to identify the chemistry of promising RHEAS alloys by using an interdisciplinary approach that combines physics-based modeling, machine learning and artificial intelligence, as well as integrated high-throughput synthesis and characterization platforms.
Arróyave said this investigation has the potential to discover alloys that can withstand the extreme environments, retain compatibility with protective coatings and can be 3D printed to make custom parts for gas turbines. All of these enhancements can result in significant energy savings in power generation and transportation.
“A major challenge that our society faces is how to do more with less. Consuming less fossil fuels while sustaining and even augmenting our energy sources and expanding our options for safe, faster and more convenient air travel is an imperative if we are to maintain our economy and keep our environment healthy,” Arróyave said.
As indicated by the Department of Energy in their news release, Phase 1 will have ULTIMATE teams demonstrate proof-of-concept alloy compositions, coatings and manufacturing processes through modeling and laboratory scale coupon testing of basic properties. As Phase 1 concludes, the findings of the teams will be reviewed and assessed for additional funding. In Phase 2, up to $14 million in additional funds will be available to selected teams.
“I believe that ULTIMATE is just the start of a broad technology development program that has significant opportunities for further development,” said Arróyave. “Finding materials capable of withstanding increasingly harsher operating conditions is an imperative in the energy, civilian aerospace and defense sectors, and the truth is that much of the science of materials under extreme conditions remains to be done. There are very exciting years ahead of us.”
To develop such ultrahigh temperature-resistant materials, particularly those that can tolerate 1,300 C or at 1,800 C with coatings, the U.S. Department of Energy recently awarded $16 million to 17 projects as a part of Phase 1 of the Advanced Research Projects Agency-Energy’s (ARPA-E) Ultrahigh Temperature Impervious Materials Advancing Turbine Efficiency (ULTIMATE) program. A team led by Dr. Raymundo Arróyave, professor in the Department of Materials Science and Engineering at Texas A&M Univeristy, has received $1.2 million to investigate a class of metals, called refractory high entropy alloys (RHEAS), that can withstand higher operating temperatures.
“Finding a ‘printable’ refractory that would enable the next-generation ultra-efficient gas turbines is quite a scientific and technological challenge that will require that we at Texas A&M University and our partners at Brown University, Oak Ridge National Laboratory, Ames Laboratory and Thermo-Calc, Inc., push our scientific know-how to the limit. We are very excited to take on this project,” said Arróyave.
Arróyave’s project, “Batch-wise Improvement in Reduced Design Space using a Holistic Optimization Technique (BIRDSHOT),” aims to identify the chemistry of promising RHEAS alloys by using an interdisciplinary approach that combines physics-based modeling, machine learning and artificial intelligence, as well as integrated high-throughput synthesis and characterization platforms.
Arróyave said this investigation has the potential to discover alloys that can withstand the extreme environments, retain compatibility with protective coatings and can be 3D printed to make custom parts for gas turbines. All of these enhancements can result in significant energy savings in power generation and transportation.
“A major challenge that our society faces is how to do more with less. Consuming less fossil fuels while sustaining and even augmenting our energy sources and expanding our options for safe, faster and more convenient air travel is an imperative if we are to maintain our economy and keep our environment healthy,” Arróyave said.
As indicated by the Department of Energy in their news release, Phase 1 will have ULTIMATE teams demonstrate proof-of-concept alloy compositions, coatings and manufacturing processes through modeling and laboratory scale coupon testing of basic properties. As Phase 1 concludes, the findings of the teams will be reviewed and assessed for additional funding. In Phase 2, up to $14 million in additional funds will be available to selected teams.
“I believe that ULTIMATE is just the start of a broad technology development program that has significant opportunities for further development,” said Arróyave. “Finding materials capable of withstanding increasingly harsher operating conditions is an imperative in the energy, civilian aerospace and defense sectors, and the truth is that much of the science of materials under extreme conditions remains to be done. There are very exciting years ahead of us.”