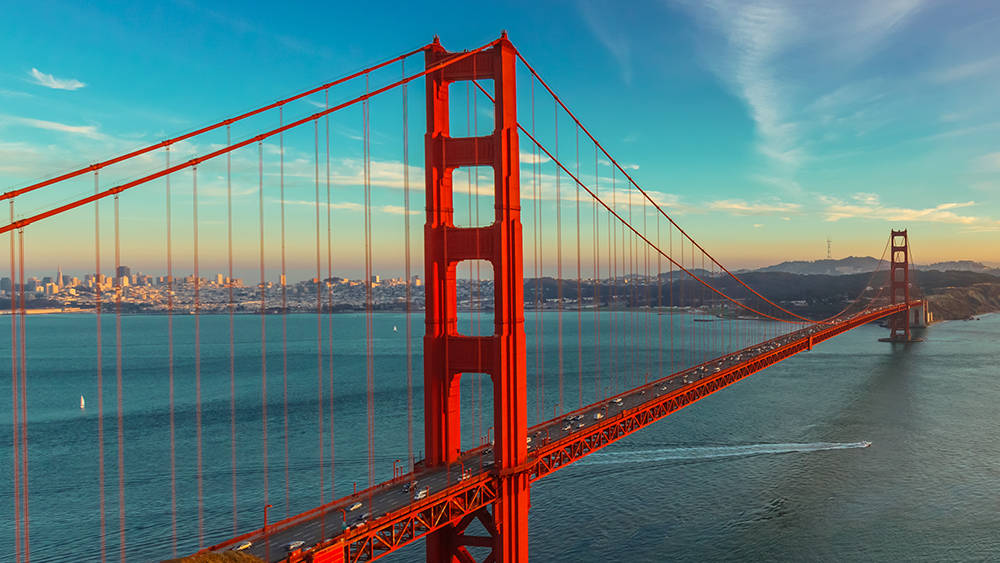
Whether the body of a commercial aircraft or the suspension beams of San Francisco’s Golden Gate Bridge, materials used for carrying heavy loads are engineered for strength and durability. But under unrelenting physical stress, structures that may appear damage-free can crack suddenly, shrouding the reasons for their failure in mystery.
Unlike pure metals, it has long been known that load-bearing materials, like steel, brass and alloys of aluminum or magnesium, have different mechanical properties in different directions. Now, Texas A&M University researchers have found that under extreme tension, this asymmetry causes load-bearing materials to deteriorate internally and, over time, develop visible cracks.
“When alloys get damaged, it’s usually very destructive since their ability to handle any kind of stress is sharply reduced,” said Dr. Amine Benzerga, professor in aerospace engineering and the director of the Center for Intelligent Materials and Structures at Texas A&M. “Our findings on the main mechanism driving failure might help make better decisions about the lifetime of alloys that are currently in use, which in turn can save a hefty amount of dollars in repairs.”
A description of their research appeared in the journal Scientific Reports.
Material failure depends on a number of factors, including the precise arrangement of the atoms and molecules that make it up. Consequently, unlike a slab of glass that shatters upon breaking, metals, in particular alloys, break counterintuitively — that is, when a piece of alloy is pulled apart, cracks are not always at 90-degree angles to the direction of the pull.
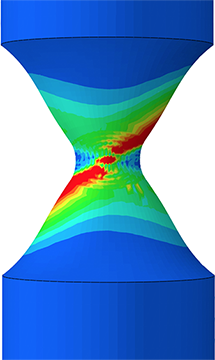
The prevalent view of the cause of this type of crack, known technically as shear fracture, has been porosity softening. According to this theory, damaging stress creates empty spaces or voids within the metal alloy, resembling holes in cheese. Under constant tension, these voids grow and join, at which point cracks form and the metal fails. However, the mechanisms that cause the voids to grow have remained murky.
Also, Benzerga and his colleagues noticed that most studies investigating the cause of shear fracture were based on experiments in which tension was applied to rectangular-shaped alloys. This shape increases the chances of shear fracture substantially, said Benzerga, giving the impression that porosity softening is the main underlying cause for failure, precluding other potential causes.
For their experiments, Benzerga and his team instead turned to cylindrical-shaped alloys and investigated if the tendency for shear fracture changed. With the new shape, they found their specimens did not always break in shear fractures.
“The fact that the shape of our specimens was influencing how often we saw shear fractures told us that something else is driving shear failure and that porosity softening was not the whole story,” said Benzerga.
To examine the cause of shear fractures, Benzerga and his team built a more sophisticated simulation model that considered porosity softening and other potential causes, including plastic anisotropy — the property by which a pull or load on a material from one direction causes damage that is different from that in another. Their simulations predicted that plastic anisotropy, and not porosity softening, triggered and propelled shear fractures.
“Our simulations were telling us something very different from the accepted theory for the cause of shear fractures,” said Benzerga. “When we completely turned off the porosity softening in our simulations and just kept the plastic anisotropy, we still got shear fractures, suggesting that plastic anisotropy drives shear failure.”
The researchers speculate that plastic anisotropy causes internal damage to the material, leading to voids. As damage continues, these voids become larger naturally, then coalesce over time and cause failure.
Benzerga noted that in the near future, their findings could help design materials that can resist shear failures better. “There are several new load-bearing materials whose mechanical properties are not fully known,” he said. “Our model now provides a framework to predict what will happen to these materials if heavy physical stress is applied to them.”
Other contributors to the research include Nithin Thomas and Joshua S. Harrington from the Texas A&M Department of Aerospace Engineering.
This research was funded by the National Science Foundation and by the Lawrence Livermore National Laboratory under Master Task Agreements.